
Official Site of Lin Huang
What I Do
Scientist
Who I Am
I received my DEA and PhD in physical chemistry from the University of Lyon 1 (France). After that, I joined the State Key Laboratory of Catalysis, Dalian Institute of Chemical Physics (China); Heterogeneous Catalysis, Institute of Chemical and Engineering Sciences, A*STAR (Singapore); Department of Chemical and Biomolecular Engineering, National University of Singapore (Singapore).


Research Interests
​
Surface organometallic chemistry, catalysis towards Fischer-Tropsch, olefin hydroformylation, C-CÂ coupling, steam reforming and lactic acid dehydration, etc.
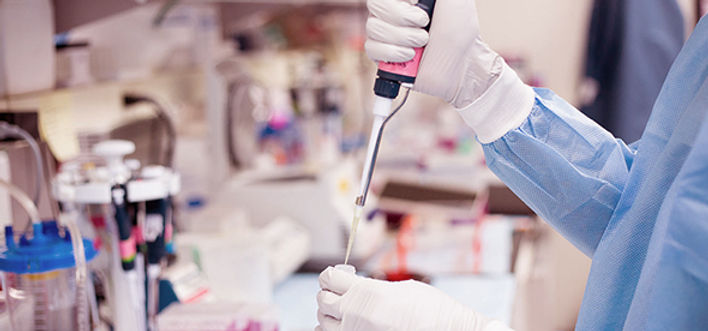
C-C Coupling
September 8, 2021
Among the various ways to synthesize arylated olefins, the construction of C(sp2)-C(sp2) single bonds through Heck coupling is probably the most attractive way. It constitutes a very selective approach of forming new C-C bonds in a single operational step by coupling aryl and vinyl halides/triflates with olefins, in order to obtain a variety of substituted olefins, dienes and other unsaturated compounds. Many of these compounds are useful as natural products and intermediates for agrochemicals and pharmaceuticals. Significant benefits of developing Heck reactions lie in the tolerance of Heck reactions toward a large variety of functional groups on both reactants and a wide availability of aryl chlorides and bromides.
​
We deeply studied SiO2-, Al2O3-, MgO-, SBA-15-, TiO2- and ZrO2-supported PdII systems derived by calcination of supported Pd(acac)2 in air and their respective supported Pd0 systems prepared by reduction of supported Pd(acac)2 in H2 for the Heck coupling of PhBr and styrene. Towards the Heck coupling of PhBr and styrene at 135 °C, supported PdII systems including PdII/SiO2, PdII/Al2O3, PdII/MgO, PdII/SBA-15, PdII/TiO2 and PdII/ZrO2 prepared by air calcination of supported PdII(acac)2 exhibited a noticeable advantage in catalytic efficiency over their respective supported Pd0 systems obtained by H2 reduction of supported PdII(acac)2 at 400 °C, in terms of the trans-stilbene yield and PhBr conversion TOF. Among all the supported PdII systems studied here, PdII/SiO2 showed the highest catalytic efficiency. The catalytic efficiency of our supported PdII systems was generally higher than that of the other reported supported Pd systems prepared by alternative ways for the Heck coupling of PhBr and styrene. The advantage of the supported PdII systems could extend to Heck coupling of other aryl bromides and olefins
The advantage of the supported PdII systems is elucidated in terms of the dependence of catalytic activity on the concentration of soluble active Pd species measured by selective scavenging of soluble molecular Pd species over a supported Pd system. Under Heck reaction conditions used, a supported PdII system is able to produce a larger amount of fine Pd particles by in-situ reduction of the supported PdII, which results in a higher fraction of molecular Pd species in solution owing to an Ostwald ripening effect. The correlation that the smaller the size of supported Pd particles, the higher the catalytic activity is further suggested for homogeneous catalysis in nature. The catalyst recyclability of the supported PdII systems under equivalent reaction conditions is dependent on the size of the supported Pd particles and the interaction between Pd particle and support. The supported PdII systems having a Pd loading of 1 % or above could give rise to a strong catalyst recyclability. At the end of Heck reaction, the contamination level of residual Pd to products could be controlled to < 5 ppm with the supported PdII systems having a loading of 1 % Pd, but increases at a higher Pd loading. Properly selecting Pd loading allows compromising between strong catalyst recyclability and low Pd contamination to products for a supported PdII system.
​

H2 Generation
September 8, 2021
H2 is considered to be the major primary energy carrier of the future and has an important role in reducing environmental emissions. With increased interest and rapid development in fuel cell technology, H2 has attracted further attention as a fuel for fuel cells. H2 is currently produced from non-renewable sources such as hydrocarbons and methanol. Due to the advent of bioethanol industry, H2 production from bioethanol through steam reforming can be a carbon-emission free process since all CO2 produced can be recycled back to the plants using solar energy. H2 production through bioethanol steam reforming also has the potential to resolve many of issues involved in H2 storage and H2 delivery infrastructure and lends itself very well to a distributed H2 production strategy. The ideal ethanol steam reforming (ESR) reaction yields 6 mol H2/mol C2H5OH as depicted in the following equation.
C2H5OH + 3H2O → 2CO2 + 6H2 (∆ Ho 298 = 173.4 kJ/mol)
The ESR process virtually consists of quite a number of frequent reaction pathways that may take place depending on the catalytic conditions. It is highly endothermic. Better performance has been conventionally observed at high temperatures of 600-800 oC, which also favor the conversion of CH4 to H2 thermodynamically. However, high temperatures impede water gas shift and thus benefit the formation of CO as a co-product. CO is a poison of the fuel cell electrodes and its concentration must be reduced to low levels below 10 ppm. High temperature ESR is energy-intensive and obviously unsuitable for the on-board applications. Therefore, reducing the reaction temperature is critically important for the efficient production of high purity H2.
​
We studied CeO2-supported Rh and Co bi-component catalysts derived from monometal carbonyls and prepared from metal nitrates for low temperature ESR by catalytic testing using a multi-channel reactor, temperature-programmed reduction (TPR), X-ray photoelectron spectroscopy (XPS), thermogravimetric analysis, H2 chemisorption, transmission electron microscopy-energy dispersive X-ray analysis (TEM-EDX), X-ray diffraction and infrared spectroscopy. Reaction product analysis showed that low temperature ESR proceeds mainly via adsorbed oxametallacycle decarbonylation (OD) and acetaldehyde steam reforming (ASR) on Rh/CeO2, ethanol dehydrogenation to acetaldehyde, ASR and water gas shift (WGS) on Co/CeO2, and OD, ASR and WGS on (Rh + Co)/CeO2. The addition of Co to Rh/CeO2 resulted in the decrease in catalytic selectivity to CO and CH4. The carbonyl-derived (Rh + Co)/CeO2 displayed marked advantage over the nitrate-prepared one, leading to CO-free H2 generation with H2 yields as high as 4.3 mol/mol C2H5OH at temperatures as low as 300 oC. Up to date, this is the lowest temperature at which high yield H2 is generated from ESR without CO contamination. Combined studies by TPR, XPS, H2 chemisorption and TEM-EDX suggested significant interaction between the Rh and Co atoms in carbonyl-derived (Rh + Co)/CeO2 in contrast to the case of nitrate-prepared one, which was assumed to promote efficiently WGS during the ESR process. A WGS-ESR bilayered catalyst system Rh/CeO2 - (Rh + Co)/CeO2 was successfully applied in CO-free and high yield H2 production from low temperature ESR.

Lactic Acid Dehydration
September 8, 2021
The conversion of biomass into fuels and high-value chemicals has received increasing attention, as climate change largely caused by anthropogenic greenhouse gas emissions related to fossil fuels has become a global concern. Biomass is abundant and contains unique building blocks, making it an attractive option to replace petroleum-based processes. Lactic acid can be produced from biomass-based cellulose via fermentation. Lactate esters can be obtained from biomass-based cellulose either via fermentation or chemocatalysis. Lactic acid has been identified by the U.S. Department of Energy as a platform substrate for future biorefineries to manufacture acrylic acid, 2,3-pentanedione, acetaldehyde, 1,2-propanediol, pyruvic acid, lactate esters and poly(lactic acid), etc. Lactate esters have been shown to be potential advantageous substrates for the production of lactide, acrylic acid and acrylate esters, etc. Products prepared from lactic acid and its derivatives are value-added building blocks for many industrial and commodity chemicals. In particular, acrylic acid and acrylate esters are very versatile monomers for major commodity chemicals with a wide range of industrial applications such as detergents, absorbents polymers, coatings, adhesives and paints, etc.
Our research was focused on vapour-phase catalytic dehydration of lactic acid to acrylic acid that is depicted in the following equation.
C2H4(OH)COOH → CH2=CHCOOH + H2O
We studied alkali and alkaline-earth metal cation co-modified NaY zeolites as catalyst systems. Long-term (time-on-stream > 55 h) catalytic performance in four repeated reaction-regeneration cycles was investigated. The best performing catalyst system showed consistently high selectivity to acrylic acid of ~84 % at different weight hourly space velocity of lactic acid ranging from 0.48 to 4.8 h-1. Most importantly, the catalyst system can still deliver a high selectivity to acrylic acid of ~82% after four long-term reaction-regeneration cycles. Investigation showed that mild etching increases defect density of the zeolite and thus leads to poor hydrothermal stability in the long-term reaction regeneration cycles.
​
We also studied neutral catalyst systems of high surface area silica-supported KNO3, and acidic catalyst systems of SiO2-Al2O3-supported KNO3. Our combined catalytic and IR monitoring results demonstrated that a dehydration reaction of lactic acid to acrylic acid proceeds efficiently with potassium lactate as the catalytic active species. The best performing catalyst system displayed good catalytic stability during 90 h of reaction in which the lactic acid conversion and selectivity to acrylic acid reached 75 and 40 %, respectively at a weight hourly space velocity of lactic acid of 1.8 h-1. We proposed reaction mechanisms for the vapour-phase dehydration of lactic acid to acrylic acid and decarbonylation of lactic acid to acetaldehyde over neutral KNO3/silica regardless of solid acid.

Hydroformylation
September 8, 2021
Hydroformylation, the addition of CO and H2 to olefins, is one of the most important syngas-related reactions. It uses the largest volume of syngas in catalytic reactions. The resultant aldehydes are versatile chemical intermediates which can be easily converted to a multitude of industrially important secondary products. Hydroformylation of an olefin (R1 to R3 organyl groups or H) is depicted in the below equation.
R1R2C=CHR3 + CO + H2 → R1R2HC-CHR3CHO + CHOCR1R2-CH2R3
The most valuable industrial applications of hydroformylation are the manufacture of propanal and n-butanal from ethylene and propylene, respectively, and the synthesis of long chain alcohols from olefins such as 1-octene and higher ones. Although cobalt-based processes govern the majority of hydroformylation reactions, Co catalysts have been challenged by Rh catalysts within the past half century. The advantages of Rh catalysts over Rh catalysts include mild conditions, high conversion rates of olefins and high selectivity to n-aldehydes. Particularly, phosphine-modified Rh catalysts find wide applications in propylene hydroformylation. Besides, cheaper noble metals like Ru have been studied and exploited to attempt to replace Rh in catalysis from economic point of view.
​
We systematically studied the following heterogeneous catalyst systems for hydroformylation and related surface chemistry.
Supported inorganic salt catalyst systems for ethylene hydroformylation:
Rh inorganic salts,
Ru inorganic salts,
Co inorganic salts,
(Rh + Co) inorganic salts,
(Ru + Co) inorganic salts;
Supported carbonyl catalyst systems for ethylene hydroformylation:
Rh carbonyls,
Ru carbonyls,
Co carbonyls,
Rh-Co bimetallic carbonyls,
(Rh + Co) carbonyls,
Ru-Co bimetallic carbonyls,
(Ru + Co) carbonyls;
Tethered Rh carbonyl catalyst systems for higher olefin hydroformylation;
Tethered Wilkinson’s complex catalyst systems for higher olefin hydroformylation.